Acciai

AISI | Werk Stoff | UNI EN | AFNOR | Cr | Ni | Mo | Ti |
---|---|---|---|---|---|---|---|
304 | 1.4301 | X5CrNi18-10 | ZGCN18-09 | 18,00 20,00 |
8,50 10,50 |
||
304L | 1.4306 | X2CrNi19-10 | Z2CN18-10 | 18,00 20,00 |
10,00 12,00 |
||
316 | 1.4401 | X5CrNiMo17-12-2 | Z6CND17-11 | 16,50 18,50 |
10,50 14,00 |
2,00 2,50 |
|
316L | 1.4404 | X2CrNiMo17-13-2 | Z2CND17-12 | 16,50 18,50 |
10,50 14,00 |
2,00 2,50 |
|
316Ti | 1.4571 | X6CrNiMoTi17-12-2 | Z6CNDT17-12 | 16,50 18,50 |
10,50 13,50 |
2,00 2,50 |
5XC min |
321 | 1.4541 | X6CrNiTi18-10 | Z6CNT18-10 | 17,00 19,00 |
9,00 12,00 |
5XC min |
Use of stainless steel
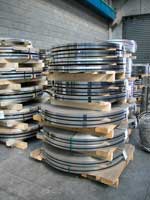
- AISI 304: Base austenitic stainless steel. Good corrosion resistance in room temperature and up to 420°C. Good welding properties.
- AISI 321: This steel has a similar composition of AISI 304 but titanium is added to obtain an inter granular corrosion resistance up to 800°C.
- AISI 304L: Similar composition to AISI 304 but a maximum carbon content of 0,03%, a characteristic that increases resistance to pitting corrosion.
- AISI 316L: Adding molybdenum together with low carbon content (<0,03%) Gives this type of steel high corrosion resistance in aggressive chemical environments and good inter crystalline corrosion resistance. Normally used up to 450°C. The mechanical properties at high temperatures are better than those of similar composition but without molybdenum.
- AISI 316 Ti: The creation of chromium carbide is avoided by the addition of titanium. This makes this steel type usable up to 800°C.
Corrosion types
General corrosion
Oxidation of the surface of the tube which causes a progressive reduction of the wall of the tube and results in a reduced mechanical resistance. This normally takes place on tubes in aggressive environments and with a coarser surface.
Tension corrosion
This happens on tubes that have mechanical stress that causes a plastic deformation of the weld or non perfect annealing. The corrosion has a high penetration speed.
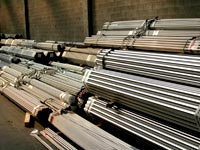
Galvanic corrosion
This takes place in contact with other metals in acid environment, that causes electrical current between the metals where one material becomes cathode and the other material anode. This area is subject to corrosion.
Inter crystallne corrosion
When the steel is used in critical temperatures, between 450°C – 850°C, A decline of chromium carbide takes place at the edges of the steel. This is often happening near the weld bead.
Pitting corrosion (pitting)
Can be caused by a number of factors:
- Ferrous contamination of the surface
- In the austenitic structure areas of ferritic/martensitic appears
- At the edges of the grains a reduction of chromium carbide
- A plastic deformation hardens the steel
- The steel mass contain non steel particles
The lack of surface passivity results in a corrosion of small or microscopical holes.
TOP